Updating natatoriums for maximum occupant comfort
Ventilation redesign
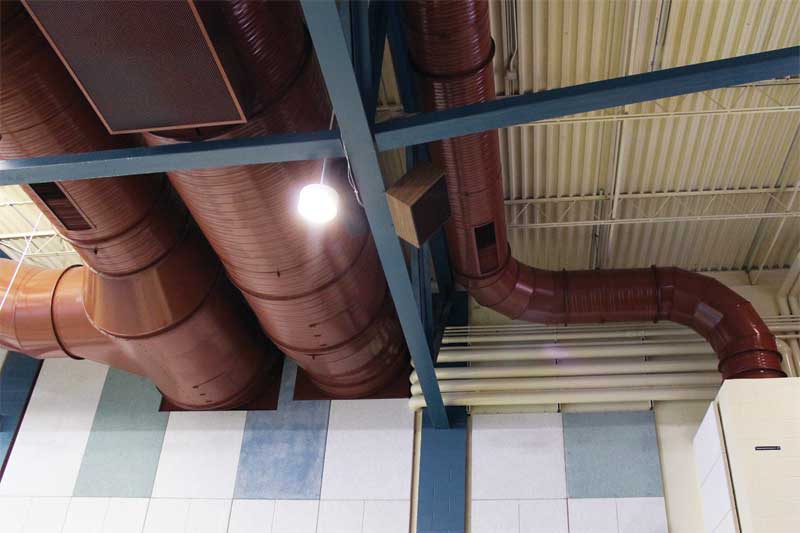
The design team replaced the existing perimeter duct system with a new, larger diameter spiral-round metal duct system. The new 1.8-m (6-ft) diameter main perimeter supply ductwork was the largest possible size for fitting through ceiling joists. This ductwork helped double the air change rate (ACH) in the room to four per hour, which complies with the four-to-six ACPH recommendations for natatorium design by the American Society of Heating, Refrigerating and Air-Conditioning Engineers (ASHRAE).
Besides facilitating more air changes, the larger ductwork and additional CFMs from the new dehumidifier greatly increased much needed airflow to all areas of the facility, right down to the breathing zone of swimmers.
Another improvement was revamping the return air system to minimize air stratification at the ceiling level. The natatorium’s original two-return air duct openings were located high on the back wall of the spectator area as a value engineered measure, because the short proximity to the original mechanical room dehumidifier below required minimal ductwork and installation labour.
Consequently, the positioning of these returns drew 27 C (82 F), chemical-laden air through the spectator breathing zone. It also created air stratification throughout the pool area and, as a result, the potential for poor IAQ during high occupancy swim competitions.
This problem was resolved in the retrofit by positioning high and low return air vents in the pool area, with a 40/60 airflow ratio, respectively. The high vents are mounted in the ceiling duct located 3 m (10 ft) above the west end of the pool and another position located 9 m (30 ft) above the southwest end of the pool. The aforementioned swimmer’s bench also contributes to the increased return air design.
Energy savings and protecting the environment
Besides temperature and RH tolerances, the new dehumidifier illustrates the technological advances of the HVAC industry. It uses energy-efficient electronically commutated (EC) motors and direct-drive fans, which are approximately 15 per cent more efficient than the belt-driven fans the previous system used.
Another advantage with respect to energy-efficiency is its ability to preheat outdoor air, virtually for free, up to 10 to 15 C (50 to 60 F) using heat recovered from the return air before it is exhausted. Avoiding the need to use utility energy to heat the air—especially during the winter in subfreezing temperatures—saves the facility thousands of dollars annually in energy costs.
Perhaps the greatest technological difference between the new and old systems is the use of glycol as a substitute for refrigerants. The original HVAC equipment used approximately 227 kg (500 lbs) of refrigerant for their dehumidification/cooling circuit and heat rejection to an outdoor condenser. Refrigeration coils and soldered copper joints typically leak at least once, if not multiple times over the life of a system. Leaked refrigerant ends up in the atmosphere. The new system uses 80 per cent less refrigerant and glycol for heat rejection. Glycol is an environmentally safer liquid, and should a leak ever occur, there is no ecological damage.
That said, the CAC has reduced its liability and dependability on refrigerants, such as R-22, a hydrochlorofluorocarbon (HCFC), which is regulated by two international agreements; the Montreal Protocol and the Kyoto Protocol. In fact, this refrigerant has been banned for manufacturing in the United States after 2020, and 2030 in Canada.
Further, the new system’s internal dehumidification refrigeration circuit is factory-sealed and tested, which eliminates the expense of on-site refrigerant-certified installers, in addition to oil migration issues.