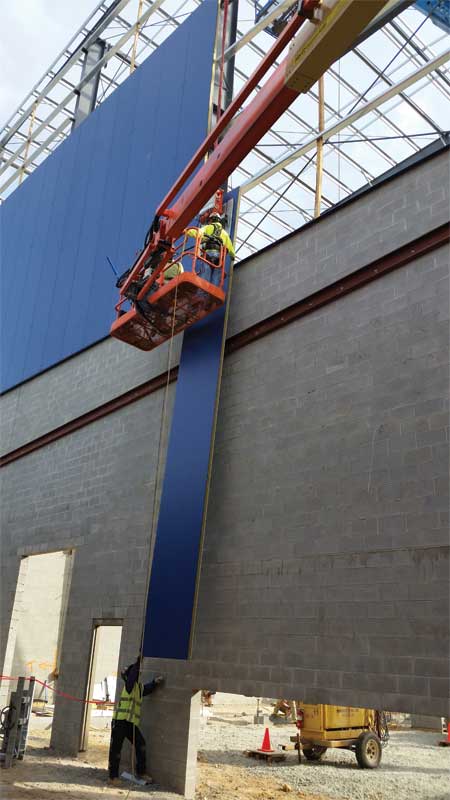
The painted metal panels also resist corrosion. For example, the renovation of a roofing system on the Pepper Geddings Recreation Center in South Carolina uses IMPs. The original batt-and-roll insulation and liner system was sagging from absorbing moisture. When roofing materials and insulation get to this point, they not only become less efficient, but also mould and mildew can become an issue, which can create health risks for the building’s occupants.
Since this facility is located in a coastal region, a special paint coats the exterior metal panels, as the roofing is subject to sea salt in the air. The interior panels also have a coating that is highly reflective, which helps reduce the number of lights required within the facility, saving the cost of lighting installation and, over time, electricity.
“The insulated metal panel is a complete system,” says Michael Walker, AIA, LEED AP, at Tych & Walker of Murrells Inlet, S.C., who specified the IMPs for the facility. “The interior panel was coated with a product that is resistant to chlorine. It offers 152 mm (6 in.) of insulation to get the R-value we wanted, and the standing seam metal roofing.”
Standing seam metal roofing is a prominent visual feature that consists of a raised interlocking seam that joins one panel to the next to form a watertight system.
Proper training can reduce labour
IMPs can easily be installed in a retrofit application following the teardown of the failing system, such as the project in South Carolina. Manufacturers offer extensive field and classroom-style training for contractors or roofers looking to offer this building material as a roofing or wall system option to their customers. Part of this training comprises a discussion or a hands-on demonstration of proper equipment available (e.g. vacuum lifts that assist with placement) which can help reduce labour on the jobsite.
The construction season in some parts of North America is never as long as it needs to be. Where IMPs can be installed year-round, other construction methods have certain limitations. For instance, tilt-up concrete must be poured in temperatures above freezing (ideally above 10 C [50 F]), which limits the building season in some areas. Other building methods, such as stud framing can be time-consuming due to the number of layers required to construct the entire system (e.g. vapour barrier, girts, insulation, and cladding typically require four passes for the builder).
Top 10 benefits of insulated metal panels (IMPs) |
---|
![]() 1. Ease of installation: Insulated metal panels (IMPs) are a composite building material with a concealed fastener system in the side joint. This provides a single source (a one-step, one-trade installation process) for the building enclosure, which also reduces the number of different trades necessary for installation. Most weather conditions do not affect IMPs thanks to its resilient nature, which allows flexibility in installation. 2. Energy efficiency: IMPs have a high thermal efficiency. Each panel contains a urethane core to help reduce building energy use and costs. 3. Design flexibility: These panels are designed for exterior and interior walls, as well as roofs. IMPs are available in multiple profiles, colours, reveals, 4. Quick construction time: IMPs comprise a foam core that is encapsulated by two sheets of steel, which serve as the building’s entire wall or roof application. This single-step installation significantly reduces construction time and aids in granting building occupancy sooner. 5. Longevity: Metal buildings not only last, they age well, too. Constructed of G-90 galvanized and AZ-50 aluminum-zinc coated steel, along with premium components and paint options, including a 70 per cent polyvinylidene fluoride (PVDF) coating, help ensure buildings standup to the elements. 6. Environmentally friendly: More than 35 per cent of the steel used in the skins of IMPs comprises recycled materials. In addition, 88 per cent of the scrap steel from panels is recycled. The R-values of insulated metal panels meet or exceed current energy codes and contribute towards credits in the Leadership in Energy and Environmental Design (LEED) Green Building Rating System. 7. Strength and durability: IMPs not only insulate buildings, but also act as a single-source water, air, vapour, and thermal barrier. 8. Low maintenance: Insulated wall and roof panels are available with paint finish warranties of up to 40 years. This means they would only need to be replaced once to achieve 60-year coverage, which is in accordance with the product category rule (PCR). Depending on local environmental conditions, the projected lifespan of IMPs can range between 50 and 60 years. 9. Cost effective: IMPs allow for the quick construction of durable, energy efficient facilities. In turn, this reduces overall installation and operation costs. With single-step installation, IMPs reduce the number of necessary trades, as well as vendors needed to manage materials, which, depending on the project, can further lower costs. 10. Fire-resistant: Manufacturers have created a mineral wool IMP to achieve one-, two- or three-hour fire-resistance ratings under the most demanding conditions. In addition to its fire-resistant characteristics, the panel provides good thermal performance and protection from the elements. |