Using various design and construction techniques designed to eliminate moisture problems
Air barrier and vapour retarder
Due to the potential for high humidity from the pool interior, both an air barrier and vapour retarder were critical to the project. Moisture vapour is transported via two different mechanisms into wall assemblies: air movement and diffusion.
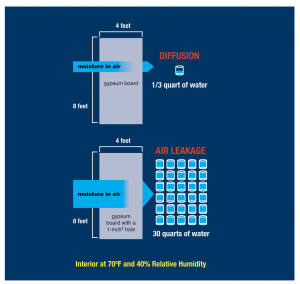
Air movement is typically the larger source of moisture problems. At 21 C (70 F) and 40 per cent relative humidity, a 25-mm (1-in.) hole will allow 90 times more water into a wall via air leakage than a 1.2- x 2.4-m (4- x 8-ft) gypsum board will via diffusion. Thus, an air barrier not only improves energy efficiency, it also serves as the first line of defence against potential moisture problems.
The vapour retarder is the second line of defence, protecting against moisture problems due to the moisture diffusion mechanism. With any design, the vapour retarder should be on the ‘warm’ side of the insulation, as it was in this project; this prevents moisture diffusion to the cold side of the assembly.
When designing an assembly, each potential condensing surface should either be warmer than the dew point or sufficiently protected from encountering moisture via diffusion or air infiltration. While multiple vapour retarders are typically discouraged, these three layers are locked into a solid, airtight assembly, preventing a moisture-trap scenario.
Insulation
Extremely humid air brings with it a high risk of condensation on walls and windows. To eliminate condensation in this project, the structure was super-insulated with R-values approximately twice the code requirements. Each cavity was filled to its entire depth to avoid any air space within the system. Not only does this eliminate the condensation potential, it also significantly reduces the heating bill for an otherwise energy-intensive building.
As the relative humidity of the indoor air rises, the difference in temperature between the air and wall surface at which condensation occurs narrows. With conditions of 25.5 C (78 F) and 80 per cent humidity, a surface temperature of 21.6 C (71 F) will cause condensation. Therefore, it was critical to strengthen the thermal weak spots in the wall. In this case, to eliminate thermal bridging at the studs, foil-faced 25-mm (1-in.) polyisocyanurate board was used on the interior of the studs adding a continuous insulation of R-value 6.5. For the glazing, high-performance, highly insulated windows were installed.