Water feature hydraulics
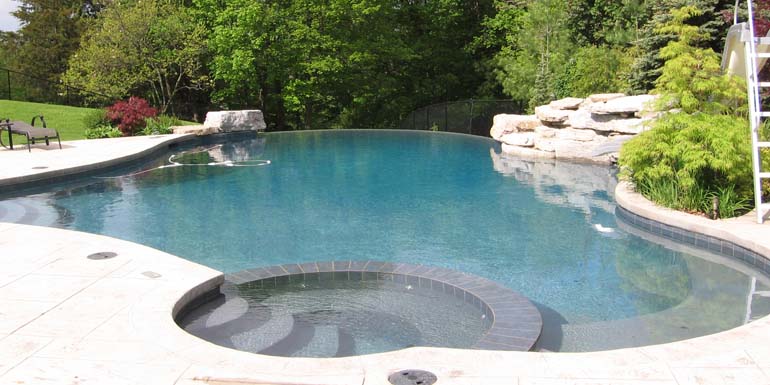
By Phil Bach
Imagine the perfect water feature; now, ask a colleague or customer to do the same and have them describe it. What are the odds the descriptions will match? Slim to none.
This is because the esthetic beauty of a water feature is truly in the eyes—and ears—of the beholder. Esthetically speaking, the perfect water feature may resemble cascading rapids or a glass-like sheet of water. It may have a large vertical drop or it may be flat and smooth, appearing almost motionless. It is, put simply, a matter of taste.
The technical beauty of a water feature, however, is much easier to describe; it is a matter of proper hydraulics. Water in any swimming pool or water feature is always in motion—or at least it should be, so it can be properly filtered, sanitized and, in some cases, heated. Controlling the water’s motion so each customer sees and hears the effects they imagined is what water feature hydraulics are all about.
Three primary considerations
To create a successful water feature, three things must be kept in mind. First, everything water encounters has an impact on its flow. This includes filters, straight and curved plumbing and other equipment, fittings, nozzles and edges water is intended to flow over. This even includes the swimmers themselves.
Second, close attention must be paid to what the client wants (and doesn’t want) to see. For example, in the case of a vanishing edge, one must carefully consider where the water will go after it leaves the pool. If the overflow will always be hidden from view, the design of the catch basin can be utilitarian. However, that same overflow could be a water feature itself when viewed from a different vantage point.
Third, variable-speed pump technology has dramatically changed water feature design parameters. Now, a single pump can provide the flow required for an infinite range of applications. When using a single- or two-speed pump, sizing and selection is critical; however, a well-designed variable-speed pump can meet many different needs (with the correct programming, of course).
Fundamentals of hydraulics
Before discussing how to achieve a particular look and the impact of new pump technology, it is necessary to understand some important elements of hydraulics.
As mentioned earlier, every fitting, elbow, length of pipe and plumbed in-line piece of equipment (e.g. heaters, chlorinators, filters, etc.) adds resistance to the system. Each of these items also has a flow requirement. For example, flow for a single spa jet or arcing laminar nozzle may be 38 litres per minute (lpm) (10 gallons per minute [gpm]), while a heater may perform best at 151, 189 or 379 lpm (40, 50 or 100 gpm), depending on the type and size. Keep in mind, the more features being added (e.g. arcing laminars) the resistance and flow requirements are additive. The key is to make sure the pump is selected (and, if relevant, programmed) to efficiently draw water through everything included in the project (e.g. dual suction ports, fittings, pipe length and size and the nozzles used to create the desired effect).
One factor that dramatically affects resistance is velocity. Water flowing at an excessive speed will dramatically increase resistance; this is also known as friction loss. If a given horsepower is necessary, make sure the size of the lines provide the most efficient and safe flows—1.8 metres per second (mps) (6 feet per second [fps]) on the suction side in particular.
The Association of Pool and Spa Professionals (APSP) recommends the velocity in pool plumbing should not exceed 3 mps (10 fps) on discharge plumbing and 2.4 mps (8 fps) on suction plumbing. The Hydraulic Institute recommends a maximum velocity of 2 mps (7 fps) for optimum hydraulic efficiency. Velocity in copper pipe should never exceed 1.5 mps (5 fps). One of the best ways to reduce velocity is to use bigger pipe. While larger plumbing is initially more expensive, it will reduce energy costs over time.
One must also remember that water vaporizes as it turns through elbow fittings and then returns to fluid as the pipe straightens. Therefore, it is good practice to leave four to five times the pipe diameter in straight pipe between any curve and the pump strainer housing. For example, when using 51-mm (2-in.) pipe, make sure there is 203 to 254 mm (8 to 10 in.) of straight pipe going to the pump.