YMCA facility upgrades its operational efficiencies
The pump
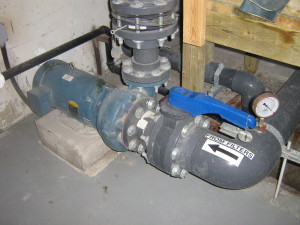
From a pump perspective, the equipment used at this YMCA was fairly simple. The existing, undersized pump was replaced with a new high-performance, 10-hp, three-phase pump with a designed flow rate of 1,419 lpm (375 gpm) at 22 m (72.9 ft) with a maximum flow rate of 2,369 lpm (626 gpm). (Note: current codes require the turnover rate for class ‘A’2 pools be no more than four hours.)
Historically, pool pumps with induction motors, which operate at only one or two speeds, have drawn more energy than is required to circulate pool water. These units must constantly operate at high speed to perform their most demanding jobs, such as running a waterfall or pool cleaner. On the other hand, it takes far less power to simply keep the pool water filtered—a difference single-speed pumps cannot address.
VFD pumps can be programmed to operate at set speeds to deliver the correct flow rate for each task they perform. This allows the pool’s pump to reduce energy consumption and ultimately reduce operating costs. VFD pumps can also be programmed to achieve turnover rates of exactly four hours, even if the filter is dirty. This allows motor speed, power, and energy to be reduced during times when the filters are clean, instead of sizing the pump to assume worst-case operating conditions.
No matter what type of pump is being used, however, slower pump speeds save energy. Slower speeds also dramatically reduce noise levels and wear and tear on other pool equipment the water flows through.
Starting with a three-phase pump is a ‘no brainer,’ when the motor on the new pump is combined with the VFD, it increases the efficiencies as well as the opportunity to capitalize on better energy savings. In fact, this facility will save approximately 35 to 60 per cent on its energy bills in comparison to using the pump originally installed. Further, it also minimizes the wear and tear on the pump.
As an aside, older pumps with their slower turnover rates are also potentially exposing bathers to more bacteria. As newer filters and/or pumps have a much faster turnover rate, bathers are exposed to fewer contaminants, and as it has been seen with Cryptosporidium (Crypto), less exposure is important to reducing the chance of a possible outbreak.
The variable-frequency drive
The VFD works much like a dimmer on a light switch. The pump’s 10-hp motor can be dropped to a lower (output) horsepower without damaging any wiring or internal mechanisms.
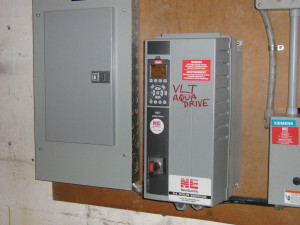
In this case, the design flow rate of 1,419 lpm (375 gpm) was able to be achieved by lowering the output to 1,400 revolutions per minute (rpm) on the drive. By reducing the motor output from 1,750 to 1,400 rpm, a 20 per cent reduction in the motor’s output was achieved. This also equates to an operating savings of nearly 55 per cent.
Hollandia explained to YMCA facility operators that with the proper hydraulics and VFD system, the facility could save up to 85 per cent in operational costs.
Specified to save energy, space, costs, and time, most VFDs are designed to be the heart of the pump room. With minimal payback time, they provide automatic energy optimization and a built-in DC link reactor to reduce harmonic noise to protect the drive. Some VFDs also offer an initial ramp, which provides acceleration of pumps to a desired minimum speed, at which time the normal ramp takes over, preventing damage to thrust bearings and overheating of the pump.
“Variable frequency drives are quite amazing,” says Deakin. “Several of the facilities where we have installed these drives have achieved an electrical cost savings of more than $10,000 per annum. The units aren’t free, but the pay back is normally less than 18 months. Some municipalities are even providing homeowners with rebates from utility companies, which makes the payback period even shorter.”