The ultraviolet (UV) light system
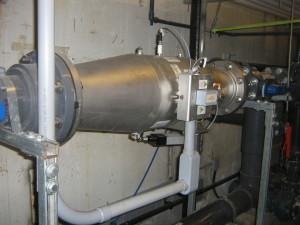
In order to continue the complete integration of the pump room, an appropriately sized UV system was installed to enhance the facility’s water and air quality. In this case, a medium-pressure UV system was incorporated into the pump room, which not only eliminates chloramines, but also offers the facility a secondary sanitation system that provides cleaner, clearer water.
Once the UV system is installed, chloramines are virtually eliminated and the air is cleared within 24 hours. In addition, the UV unit contributes to reducing the facility’s operating costs as 30 to 40 per cent less chlorine is being used.
The auto-water level control system
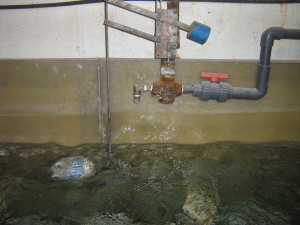
The MOH also requires the installation of an auto-water control system. This system automatically replaces water that is lost to evaporation and bather carry out (i.e. splash out). As mentioned earlier, the MOH requires facility operators to replace 20 L (5.2 gal) of water per bather, per day. Unfortunately, however, this regulation was put into place before the technological advancements mentioned in this article (e.g. filters, chemical controllers, and UV sanitation systems) were available for pools.
Although an auto-water control system was integrated into the YMCA facility’s pump room, there has been growing interest in the revision of this requirement as current technologies have made it redundant.
A green facility
With many municipal and YMCA-type pools struggling to keep their doors open, the integration of all components in the pump room is paramount to ensuring the lowest possible daily, weekly, and yearly operating costs for these facilities.
After hiring Hollandia as the designer/builder to update the Woodstock YMCA and implement these types of operational changes, facility operators realized how much their operating costs would be reduced. Plus, the additional benefits to the facility’s water and air quality would help it remain competitive among the many other private athletic facilities and municipal pools in the region.
In fact, the Woodstock YMCA even promotes the pump room integration upgrades it made, showing that it is a ‘green’ facility and a good steward to the environment and community. By not wasting water and eliminating harmful byproducts, which eventually end up in the community’s water system, the facility is doing its part to be a sustainable part of the community.
“Aquatic facility operators and managers should take the time to look at the big picture as they might be surprised about how some upfront investment can have a huge impact on their operating costs, and possibly even change their entire business model,” says Deakin.
Mike Fowler is the commercial marketing and sales manager for Pentair Water Commercial Pool and Aquatics in Sanford, N.C. He has been with Pentair since 1992, starting his career in the technical services department at Purex Pool Products. Fowler has held many managerial roles within the company, including marketing, accounting and products. He can be reached via e-mail at mike.fowler@pentair.com.